Cutting-edge Methods to Fillet Weld Examination and Testing: Enhancing Weld Quality and Compliance Criteria
In the world of welding, the top quality and honesty of fillet welds play a vital function in making sure the structural soundness and dependability of various commercial elements. With the consistent drive for improved effectiveness and compliance with stringent criteria, the exploration of innovative techniques to fillet weld examination and testing has become imperative. As sectors develop, the typical techniques might no more be enough in meeting the needs of contemporary welding applications (Gauge Fillet Weld). By accepting advanced innovations and methods, a new perspective of opportunities emerges in the realm of weld top quality assessment and adherence to conformity criteria.
Advanced Non-Destructive Screening Approaches
Utilizing state-of-the-art innovations, advanced non-destructive testing techniques play an important function in guaranteeing the integrity and high quality of fillet welds. These approaches, such as phased variety ultrasonic testing (PAUT) and magnetic fragment screening (MPT), deal comprehensive insights into the weld's interior framework without causing any type of damage to the material. PAUT, as an example, utilizes several ultrasonic aspects to check the weld from numerous angles, supplying a thorough visualization of potential problems like lack of fusion or splits.
By using these sophisticated non-destructive screening methods, weld assessors can properly analyze the high quality of fillet welds, making certain conformity with market requirements and policies. The capability to spot imperfections early on not only enhances weld quality however additionally stops expensive rework or failings in architectural integrity, underlining the relevance of these cutting-edge testing techniques in welding inspections.
Robotics and Automation in Inspection

The integration of robotics and automation has actually reinvented the evaluation process for fillet welds, improving performance and accuracy in high quality assessment. Robotics provide specific control and repeatability in evaluating welds, making certain consistent and trustworthy outcomes. Automated systems can be programmed to comply with specific inspection courses, guaranteeing thorough coverage of welds and lowering the danger of human mistake.
Robotic assessment systems outfitted with innovative sensing units can detect and measure weld functions with high precision, giving comprehensive information for analysis. These systems can recognize defects such as cracks, lack of combination, and porosity, allowing punctual corrective actions to be taken. Additionally, robotics and automation permit real-time information collection and analysis, providing immediate responses to operators and assisting in fast decision-making procedures.
In addition, making use of robotics and automation in fillet weld evaluation enhances total efficiency by lowering inspection times and enhancing evaluation throughput. By streamlining the evaluation procedure, suppliers can make certain weld quality and compliance requirements are met successfully, inevitably bring about set you back savings and enhanced product quality.
Making Use Of Artificial Intelligence for Evaluation
Fabricated intelligence plays a crucial function in improving the effectiveness and precision of analysis in fillet weld examination processes. AI algorithms can quickly process large amounts of information from weld evaluations, identifying defects or inconsistencies that might be testing to recognize with the naked eye.
Furthermore, AI systems can pick up from previous assessment data, continually improving their capacity to identify possible defects and discrepancies in fillet welds. This adaptive understanding capacity boosts the total quality assurance procedure, minimizing the chance of human mistake and making certain that welds meet the required criteria. By integrating fabricated intelligence into fillet weld analysis, industries can attain higher degrees of efficiency, consistency, and conformity in their check out here assessment methods.
Portable Equipment for On-Site Assessment
Enhancing field evaluation performance, the fostering of mobile devices reinvents on-site assessment processes for fillet welds. These devices offer adaptability and convenience, allowing examiners to carry out extensive evaluations in different locations, consisting of challenging or remote environments. Portable devices such as ultrasonic testing tools, magnetic fragment inspection devices, and digital radiography systems provide real-time data and high-resolution imaging capacities, allowing fast decision-making and immediate feedback on weld top quality.
One significant benefit of portable devices is their capacity to simplify inspection procedures, minimizing downtime and boosting total performance - Gauge Fillet Weld. Examiners can easily deliver these tools to different job websites, getting rid of the need for transferring hefty machinery or elements to off-site facilities. Furthermore, the portability of these devices promotes cost-effectiveness by decreasing transportation expenses and increasing evaluation timelines
Furthermore, making use of portable tools for on-site examination promotes proactive high quality control steps, as inspectors can without delay identify and address any type of prospective welding problems or inconsistencies. By integrating these cutting-edge modern technologies right into on-site assessment techniques, welding experts can ensure conformity with market requirements and enhance weld top quality, ultimately causing their explanation improved architectural integrity and security in various welding applications.
Integration of Information Management Equipment

Having actually maximized on-site assessment procedures with the use of mobile devices, the next phase includes the seamless combination of information management systems to better enhance performance and information analysis capabilities in fillet weld inspection and testing. By incorporating information monitoring systems into the evaluation process, companies can simplify data collection, storage, and evaluation. This combination enables real-time surveillance of weld top quality, prompt identification of issues, and prompt decision-making to rectify any kind of issues that might occur throughout the inspection process.
Information management systems play an important function in streamlining examination information, helping with simple accessibility for authorized personnel, and making certain data stability and security. Via the assimilation of these systems, assessors can generate detailed records, track historical information for trend evaluation, and boost general procedure efficiency. Additionally, the integration of information management systems visit the website enables seamless communication between different stakeholders associated with the assessment process, promoting cooperation and improving general quality assurance measures. Eventually, the assimilation of data monitoring systems offers to elevate the standards of fillet weld assessment and testing, making certain compliance with market regulations and improving weld high quality.
Conclusion
Finally, innovative techniques to fillet weld examination and screening have actually significantly boosted weld top quality and conformity requirements. Advanced non-destructive screening techniques, robotics, automation, fabricated intelligence, portable tools, and information monitoring systems have actually changed the method weld evaluations are carried out. By using these technologies, industries can make sure that welds fulfill the required top quality criteria and regulations, inevitably enhancing total efficiency and security in welding procedures.
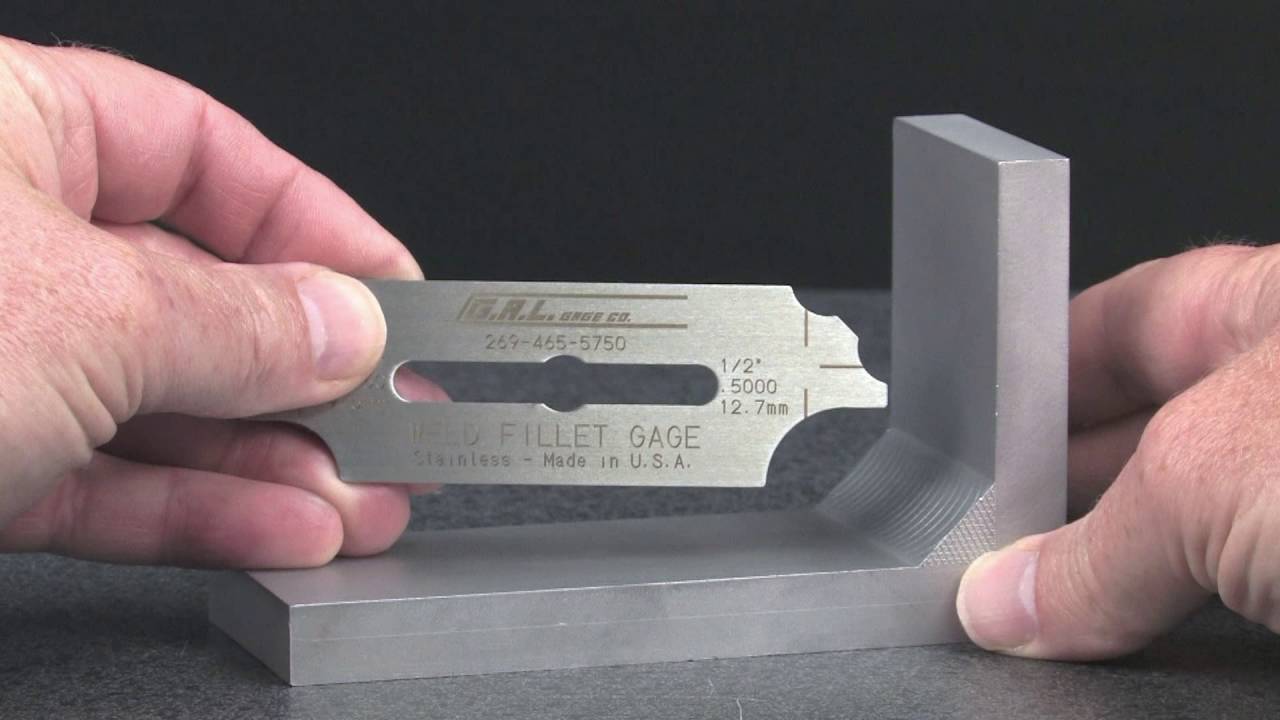
Having enhanced on-site assessment procedures through the utilization of mobile devices, the next stage includes the seamless assimilation of information management systems to even more enhance efficiency and information evaluation abilities in fillet weld evaluation and testing. Eventually, the assimilation of information monitoring systems offers to boost the standards of fillet weld assessment and testing, making sure conformity with sector guidelines and boosting weld high quality.
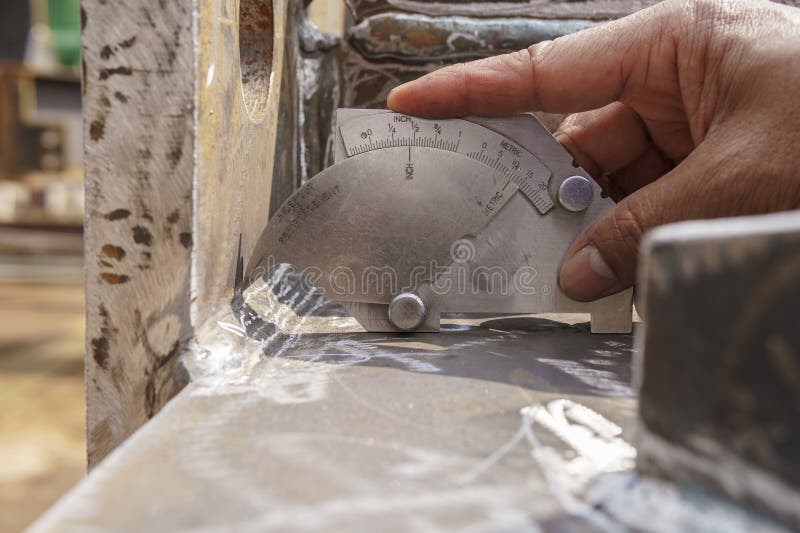
Comments on “Gauge Fillet Weld Basics: Best Practices and Common Mistakes”